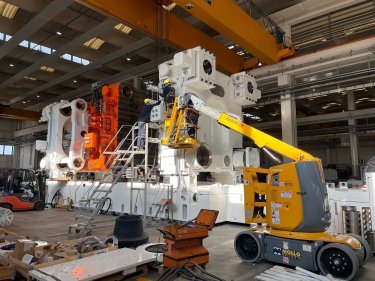
Tesla Giga Press
Photo from Pinterest;
https://pin.it/U9MMqT8M4
Academic assignment of the class (266-751309)
Tesla’s rise to prominence as a trailblazer in the electric vehicle market is deeply rooted in its unwavering commitment to leveraging cutting-edge technologies and driving continuous innovation. The company’s notable achievements, such as the establishment of gigafactories and the development of advanced batteries, underscore its position as a pioneer in the automotive industry. Now, Tesla is poised to push the boundaries even further with the incorporation of a groundbreaking technology known as the Gigapress, signifying a strategic move to streamline and enhance their car manufacturing processes.
At the heart of Tesla’s innovative journey lies the Gigapress, currently holding the title of the world’s largest die casting machine. Its staggering specifications include a weight of up to 430 tons and an imposing clamping force of 61,000 kN, making it an engineering marvel. These gigantic die casting machines, comparable in size to houses, have the capability to cast exceedingly large components. What sets Tesla apart in this narrative is its distinction as the first company to place an order for the Gigapress, a move that has captured the attention and curiosity of those associated with the die casting industry.
The Gigapress owes its name to Ricardo Ferrario, the General Manager of the IDRA Group, which introduced this revolutionary technology in late 2018. While it found its place in the group’s catalog early on, it wasn’t until late 2020 that Tesla commenced its use, deploying a customized OL 6100 CS Gigapress for production. Notably, prior to Tesla’s adoption, IDRA had already received the first order for a 5500-ton high-pressure die casting (HPDC) machine in 2019. Tesla’s commitment to innovation and scale is further emphasized by Jerome Guillen, the President of Automotive at Tesla, who disclosed the company’s ambition to create a colossal machine for producing full-size cars, drawing an intriguing analogy to the manufacturing process of toy cars.
Elon Musk’s announcements in 2020 and 2021 shed light on Tesla’s journey with the Gigapress. In April 2020, Musk revealed the acquisition of two enormous die casting machines to manufacture chassis parts for the Tesla Model Y. Later, in January 2021, he announced that the rear chassis of the highly anticipated Tesla Cybertruck would be cast using a Gigapress with an astonishing clamping force exceeding 8,000 tons. Tesla’s commitment to Gigapress technology is evident in the successful installation of three Gigapresses in Shanghai and two in the Fremont factory, with indications of additional installations in recent times.
Understanding the intricate workings of the Gigapress reveals a complex yet highly efficient die casting setup. The process involves utilizing two sets of ovens for handling the aluminum alloy, with one serving as a melting oven powered by natural gas operating at 850 degrees Celsius and the other as a storage oven for the liquid metal heated by electrical power, maintaining a temperature range of 750 to 850 degrees Celsius. The core of this colossal setup, functioning similarly to regular high-pressure die casting equipment but on an enormous scale, ensures the efficient production of large and intricate components.
Critical components within Tesla’s Gigapress setup include a 4000-liter tank, manufactured by Fondericks, a Swiss company that pioneered vacuum technology for high-pressure die casting. This tank plays a pivotal role in creating a vacuum inside the mold. The quenching tank, another integral component, rapidly reduces the temperature of the casting to a desired limit, unlocking specific material properties for the metal casting. The process also involves a mechanical trimming press and laser trim for cutting excess metal from the casting, contributing to a recycling system that efficiently utilizes scrap metals for subsequent casting cycles.
The working principle of the Gigapress unfolds in a sequence of meticulously orchestrated steps. The process begins with the melting of aluminum ingots and cutoffs from the previous casting cycle in an oven at 850 degrees Celsius. Following this, impurities are removed from the surface, and the liquid metal is conveyed into another enclosed oven using heated pipes. Maintaining a temperature range of 750 to 850 degrees Celsius, this second oven, filled with nitrogen gas to prevent oxide formation in the molten aluminum, further purifies the metal using argon gas, rotary degasser, and a silicone carbide filter before each casting cycle.
Ensuring the smooth operation of the Gigapress involves the application of 35 milliliters of soybean oil in a thin layer by a robot to lubricate the dye surfaces. The vacuum system creates about 50 millibars of pressure inside the mold cavity, facilitating the transport of molten aluminum from the holding oven to the shot chamber of the Gigapress. Here, a high-speed plunger injects the molten metal into the cavity. The plunger, lubricated with eight milliliters of oil before each shot, ensures the casting remains inside until it solidifies. Upon completion, the casting is ejected from the dies at 400 degrees Celsius and swiftly placed in a quenching tank to rapidly reduce its temperature from 400 to 50 degrees Celsius, addressing defects and enhancing material properties.
The Gigapress journey continues with the cooling of the open die to 185 degrees Celsius and thorough cleaning with robots, preparing it for the next cycle. The subsequent casting cycle, commencing one to two minutes after the current one finishes, involves the cutting of raw castings into approximate dimensions using a mechanical trim press. The scrap aluminum undergoes recycling through a scrap metal shredder and is then added back to the oven. The main casting undergoes a meticulous inspection with an X-ray to identify internal defects, followed by further refinement using a laser trim and drilling with a CNC machine for fittings. The finished casting’s accuracy is ultimately verified with a coordinate measuring machine.
The Gigapress technology holds the promise of transformative possibilities, even in its nascent stages. While not fully implemented, the potential advantages are already discernible. The Gigapress is poised to significantly enhance the production efficiency of large and complex products, allowing manufacturers to cast large single components instead of numerous smaller parts. This streamlined approach virtually eliminates assembly operations, resulting in substantial savings in time, labor, and production costs. Furthermore, casting larger single pieces enables the creation of lightweight structures while imparting additional strength to the casting. It also reduces the likelihood of alignment issues during assembly, ensuring high-quality castings.
A notable advantage of the Gigapress is its potential to minimize the need for robots in production, accompanied by a significant reduction in body shape size, thereby contributing to savings in land use. As of now, the major application of the Gigapress appears to be in automotive castings, with Tesla actively exploring its utilization in the Model Y. The company aims to replace 70 individual castings in the rear body structure of the Model Y with a single Gigapress-produced component. Plans are also underway to cast a front chassis component using the Gigapress.
The transformative potential of the Gigapress technology is undeniably captivating, yet its widespread adoption and sustainability remain subjects of exploration and scrutiny. As a relatively new technology, researchers and industry experts must delve into aspects such as efficiency, cost, stability, and reliability associated with the Gigapress. The industry’s historical skepticism towards embracing new concepts suggests a potential gradual acceptance and implementation by other manufacturers.
Despite potential hurdles, Tesla’s successful trial runs on the Model Y rear chassis indicate progress, even with numerous iterations required to reach that point. As manufacturers gain more insight into the technology, the design process for mega casting is anticipated to become more streamlined.