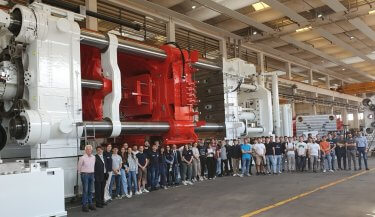
The invention of Giga Press (Die Casting Machine)
When we get the big casting machine, it’ll go from 70 parts to 1 with a significant reduction in capital expenditure on all the robots to put those parts together. Said Elon Musk. The Giga Press generally known as the largest die casting machine in the world in 2020, initially by Idra Group in Italy. […]
When we get the big casting machine, it’ll go from 70 parts to 1 with a significant reduction in capital expenditure on all the robots to put those parts together. Said Elon Musk.
The Giga Press generally known as the largest die casting machine in the world in 2020, initially by Idra Group in Italy. In late 2020, Tesla customized OL 6100 CS Giga Press for the production of chassis parts for the Tesla Model Y. This success leads Tesla to become one of the biggest car innovations in the world by using new technology and high quality of battery for their cars.
-
General information of machine
It is a high-pressure die casting machine, a process in which molten metal is injected into a mold at high pressure. which has a mold closing force (Clamping Force) of up to 55,000 to 61,000 kilonewtons (5,600 to 6,200 tf)
The Giga Press uses two sets of ovens for handling the aluminum alloy. One functions as a melting oven powered by natural gas and operates at 850°C temperature. Another oven stores the liquid metal heated by electrical power and operates at 750 to 850°C temperature. It is the core of the whole setup or the die casting mechanism. It has a similar construction to any regular high-pressure die casting equipment and functions like one, except that it is enormous in size.
After 2019, Tesla successfully signed a contract with Idra to deliver another Giga Press to Tesla electric car factories around the world.
-
Fremont, America
-
Berling, Germany
-
Shanghai, China
-
Texas, America
Advantages:
-
Improve the production efficiency of large and complex products.
-
Allow manufacturers to cast large a single component as opposed to numerous smaller parts.
-
Great savings in time, labor, and the cost of production.
Disadvantages:
-
It is mostly impossible to repair small parts, instead it needs to be replaced entirely which is cost prohibitive.
-
A challenge of maintaining unknown elements during manufacturing.
-
There are a lot of doubt of how firm apply sustainability to those technique.
In conclusion, Giga Press has alternated perspective of traditional car body (unibody) design and streamlining manufacturing by eliminated 1600 welds, removed 300 robots from the assembly line, and reduced capital investment and floorspace. The reduction of component parts is resulted in lower weight of the car.
This article is a part of the class “751309 Macroeconomics 2”
Supervised by Asst. Prof. Napon Hongsakulvasu
Faculty of Economics, Chiang Mai University
This article was written by
Kawisara Kongla, 651615002
references:
https://blink-drive.com/index.php/2021/01/24/tesla-giga-press-world-evolution/
https://www.linkedin.com/pulse/giga-press-transforming-teslas-manufacturing-danilo-onorino-cbcoe